RAMPF has the solutions for your resin system needs.
By investing the time to fully absorb and understand your needs,
we can deliver the most effective solutions, customized just for you.
Browse Our Products
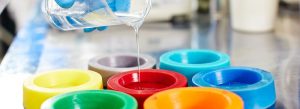
Castable Urethanes
Experience the excellence of RAMPF’s castable urethanes. Our state-of-the-art processing ensures consistency and uniformity for the toughest applications.
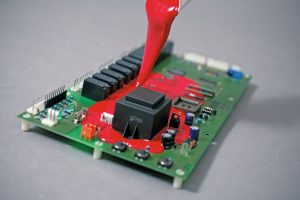
Electro Casting Resins
Innovative Solutions for Sealing, Bonding, Casting, and Protecting Our polyurethane, epoxy, and silicone-based products – RAKU PUR, RAKU® POX, and RAKU® SIL – offer a
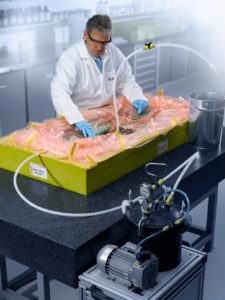
Laminating & Infusion Systems
Epoxy Laminating System: Temperature resistant, unfilled epoxy system with slow or fast reactivity. Key Properties: -Low viscosity -Excellent wetting properties -Good cure at room temperature
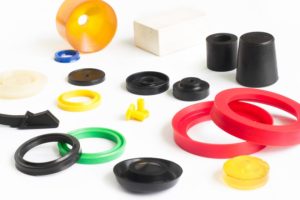
Mold Making Materials
A full range of RTV Silicone Rubbers is available from RAMPF for casting durable molds that are suitable for building accurate prototypes for a variety
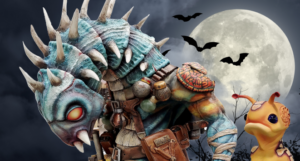
Sculpting Epoxy
RAMPF’s new sculpting epoxy adheres very well to metal and fiberglass sub structures and wood. It is easy to sand and paint, and textures can
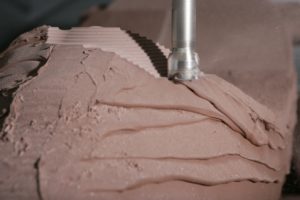
Seamless Tooling
Advantages of process -Homogeneous and seamless surface of any size part / model -Cost-effective supporting structure -Easy processing through thixotropic adjustment, no slump on vertical
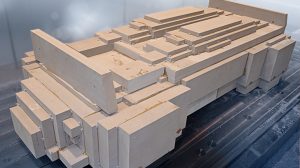
Tooling Boards
RAMPF Tooling Solutions – the world’ largest producer of styling, modeling, and working board materials. Dimensionally stable Superb edge strength Compatible with all paints, release
Talk to the team
Have questions about a product? Want something custom made just for you?
Get in touch with one of our expert sales-representatives for more information about our products.